要做好充电桩必须熟知充电桩散热原理及散热解决方案
首先,我们先来简单了解一下充电桩的结构及材料的应用。
充电桩主要由内部元件、外壳材料、连接装置及电线电缆等组成。内部元件的散热风扇一般采用加玻纤的PBT或PPE;电源外壳一般用阻燃尼龙;断路器一般用无卤阻燃尼龙材料;直流桩内部金属支架目前可以用超高玻纤增强材料或阻燃增强尼龙材料来代替。外壳材料一般选择耐候性、阻燃性较好的材料,并且要方便配色,搭配建筑的材料。我们可以采用金属外壳也可以是非金属外壳。金属外壳多指钣金外壳,塑胶外壳多用PC、PC/ABS。而插座一般选用电绝缘性优良的阻燃PET、PA66系列。电线电缆的性能要求是:耐油耐候阻燃环保柔韧性好,目前国内采用的是CQC的标准。
充电桩散热方案设计的重要性
建设充电设施的目的是让待充电车辆在较短时间内补充50-60%以上的电能,在实际应用中一般电动汽车使用直流快充,可在1~2H内充满,而我们家中所使用的交流电只能使用慢充模式需要6-8h才能充满。新能源汽车能否推广的一个重要因素就是使用过程的便利性,因此对于电动汽车充电需求来说当然是越快越好,但是随着充电速度加快,电流和电压也会直线增高,这就导致了充电桩电感模块功率增大。电感模块、电源模块等元件热量快速且大量地产生。
充电桩充电过程中产生的热量有多大?
为了直观的给大家了解充电桩在正常工作时产生的热值,我们以功率为60KW充电桩和通信电源柜做对比:
目前行业主流模块效率标称95%,以60KW系统为例,仅模块散热量就达到60*0.05*1000=3000W,这意味着充电桩在充电过程中,产生的热量是同等体积条件下通信户外机柜散出热量的3倍。
由此可以看出充电桩在充电过程中产生热量之大,若不及时散出,会造成极大地安全事故,因此,散热问题是充电桩系统推广建设必须解决的难题之一!

首先我们介绍一下温升要求:
充放电装置在额定负载下长期连续运行,内部各发热元器件及各部位的温升不超过表中的规定。
表 内部元器件极限温升
部件或器件 |
极限温升 |
功率开关器件 |
70 |
整流变压器、电抗器B级绝缘绕组 |
80 |
与半导体器件的连接处 |
55 |
与半导体器件连接处的塑料绝缘线 |
25 |
母线连接处铜与铜 铜搪锡----铜搪锡 |
50 60 |
首先我们介绍一下温升要求:
充放电装置在额定负载下长期连续运行,内部各发热元器件及各部位的温升不超过表中的规定(表)。
目前充电桩常规采用的散热方式多为散热风扇。
优点:成本低,安装简便,能耗较少;
缺点:户外灰尘易进入柜内污染精密元器件;若发热体散热不强,热量易积聚在发热体内,即使外界散热力度再大,效果都有限;不利于轻型集成设计。并且箱体的进出风口会带来尘埃、腐蚀性气体、湿气等干扰。
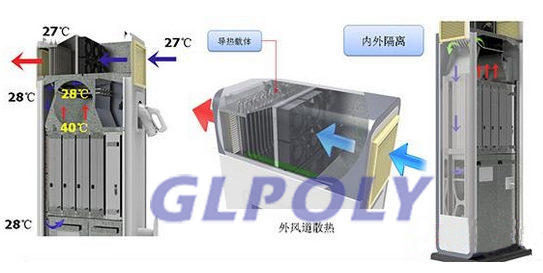
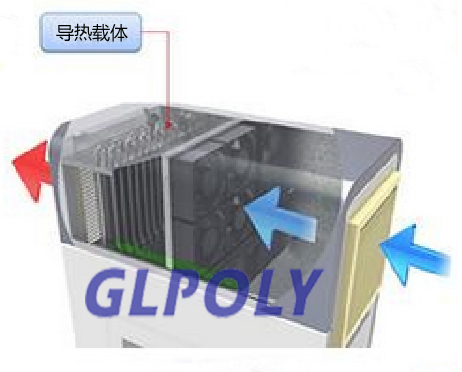
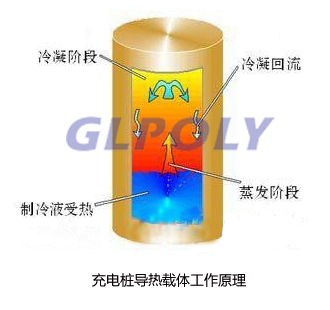
充电桩导热硅胶片的应用:
导热硅胶片可将电感模块内发热部件快速传导至电源铝制外壳,从而降低电感模块内的温度;同时,利用充电桩导热硅胶片高弹性的特点起到防震减震的作用。
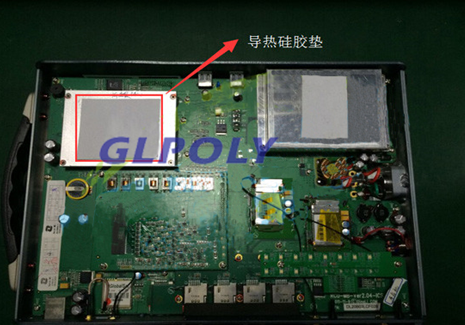
核心芯片导热硅脂的应用:
纵观任何电子设备芯片无疑是最大发热量部件,而芯片与散热器两者的缝隙存在热阻,影响芯片散发出的热量的传导。由于导热硅脂是胶状物,能很好地填满这些缝隙,加之其良好的导热性和绝缘性,增大了散热面。因此成为了充电桩各部件芯片导热材料的最佳选择。
灌封胶在充电桩上的应用:
许多充电桩需要建设在户外使用,防水等级要求极高。在改建或装配的充电桩用时,使用高效的阻燃导热性灌封硅胶。其防水,防尘,耐高低温等诸多特性可以保护电源模块及其他电子元器件的灌封保护。,更为重要是提升了其安全性和使用寿命。
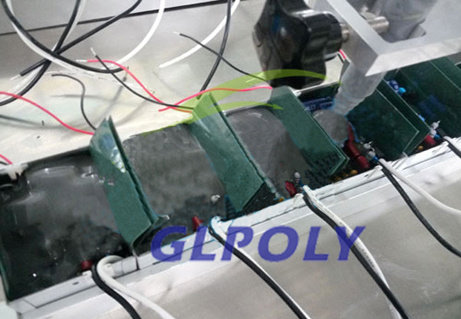
GLPOLY应用于充电桩上的高分子导热材料有充电桩导热硅胶片XK-P系列,导热系数1.0-7.9W,具有高导热、高绝缘、超高耐电压、低渗油率、高可靠度、高压缩及回弹性、柔软自黏、易施工等特性;充电桩绝缘导热薄材XK-F系列,导热系数0.8-5.8W,厚度为0.1-0.3mm,此产品高导热,高绝缘,低热阻,表面的高平坦性即使低压下使用都可以达到低接触热阻;另外还有非硅导热硅脂及非硅导热灌封胶等,欢迎来电咨询0755-27579310.